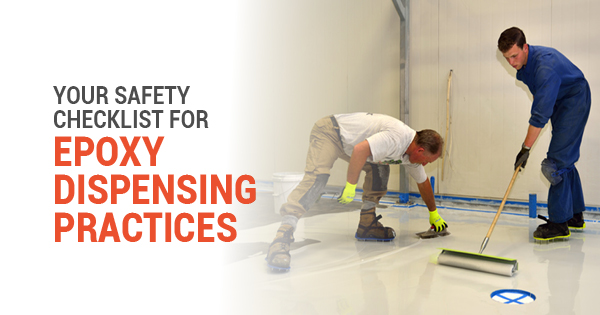
Countless industries rely on adhesive dispensing solutions to create the products on which the public consistently relies. But working with materials like epoxy can come with certain risks. If handled incorrectly, this material (or the equipment through which it’s dispensed) could present a health risk to workers. That’s why it’s so essential to prioritize safety during every step of the process. Today’s post should act as a general checklist that can keep your employees safe and the quality of your products high.
Ensure Proper Ventilation
Epoxy resins contain chemicals, and when those chemicals are mixed, strong reactions may occur. If safety procedures are not followed, these chemical reactions can result in physical irritation, allergic reactions, and respiratory issues. The health risks may be even more pronounced for pregnant women. Therefore, it’s vital to safeguard your employees with the right kind of ventilation when using these fluid dispensing systems. Local exhaust ventilation setups should be used during surface preparation and throughout the entire process to prevent chemical vapor buildup. Dilution ventilation (e.g., using fans and open windows to bring in fresh air) can be a welcome complement, providing that they do not redirect the chemical vapors into an area that could harm others.
Wear the Proper Gear
When in good working order, epoxy dispensing equipment should not pose an inherent danger to the worker. But it’s important to note that the finer points of adhesive dispensing can pose certain risks for those who do not wear the correct protection. After all, potting compounds can reach 200 degrees Celsius or higher during the curing process. That’s enough to make anyone a bit nervous about handling these materials and the equipment used to dispense them. While workers should always follow manufacturer recommendations pertaining to protective gear, it’s typically a good idea to wear chemical goggles to protect the eyes, laminate or rubber gloves for the hands, aprons and coveralls (along with long sleeves) to safeguard the skin and body, and secured footwear such as boots. Full-face respirators may also be utilized, as long as they comply with manufacturer and OSHA standards.
Train Employees Correctly
When working with epoxy dispenser pumps, ventilation and protective gear will certainly help. But if a worker isn’t trained adequately, these measures could be all for naught. Employees should be taught to use disposable containers for mixing and pouring (if applicable) to eliminate the need for reusable bowls and subsequent injury from clean-up. Employees must be trained to keep work areas free of clutter and to wipe up spills in the recommended manner. Tools should be cleaned properly after use and workers’ clothes should be changed promptly following a shift. Your organization should supply all of the necessary time and supplies required to keep the workspace a healthy and safe one. You should also make it a priority to train on an ongoing basis and to ensure all workers understand what it takes to comply with industry regulations and your organization’s safety policies.
Most of us rely on adhesive dispensing in some way or another. This process is part of our daily lives, either directly or indirectly. But in order to keep productivity high, your facility needs to make safe dispensing practices a priority. Often, that starts with choosing the best equipment for your needs. For more on how we can help, contact us today.